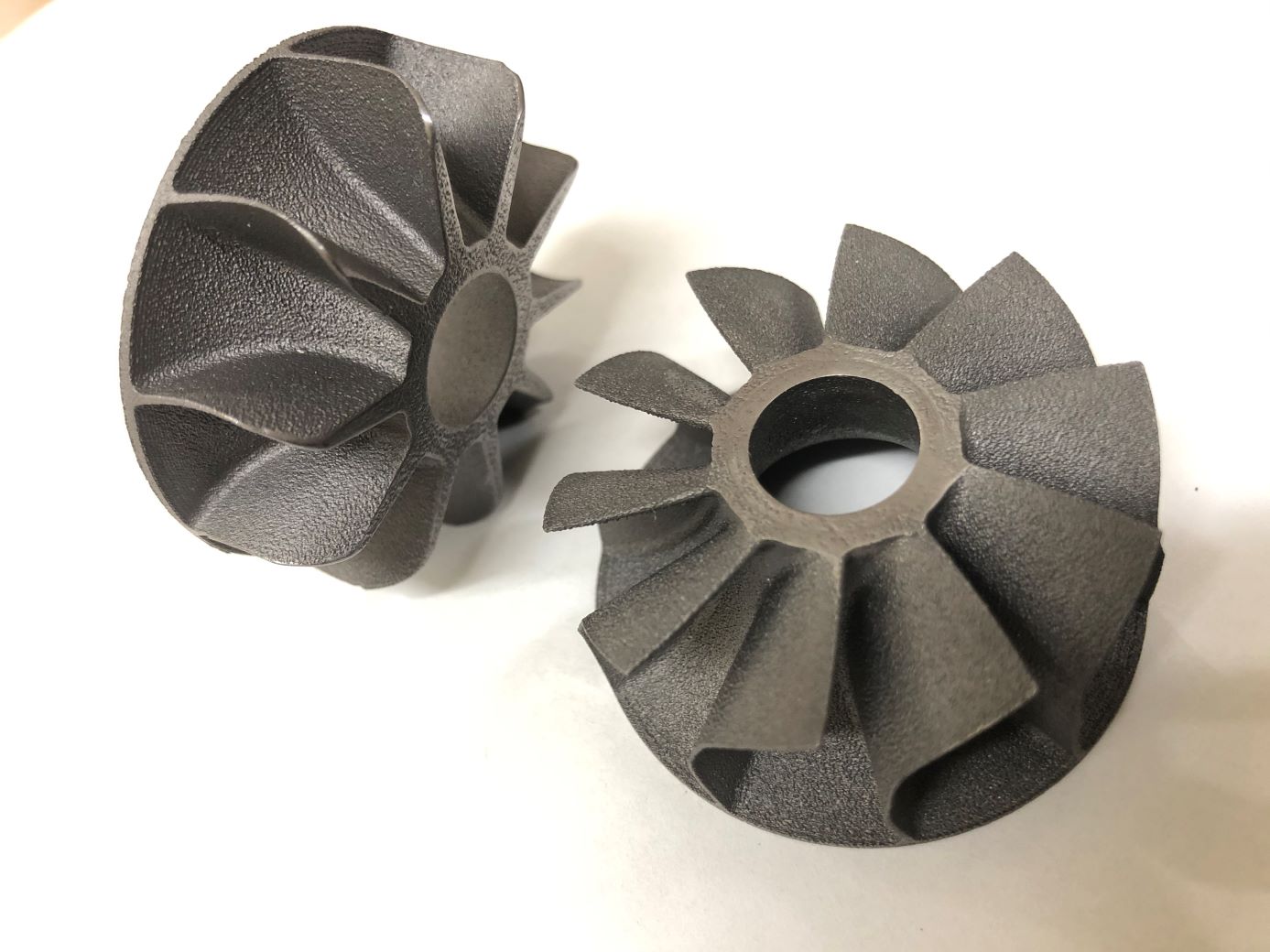
Laser – Powder Bed Fusion Printing
Laser – Powder Bed Fusion (L-PBF) is a prominent method in additive manufacturing for metal components, enabling the production of various printed parts. This technique utilizes layers of spherical metal powders that are melted and fused by a laser, creating fully dense parts with precise dimensions and excellent surface finishes. It is particularly well-suited for complex geometries and materials that can be used in their printed state.
At Elmet Technologies, we specialize in crafting custom powders and optimizing printing parameters to manufacture high-density refractory metal components for a range of applications. Our adaptable production capabilities allow us to achieve quick turnaround times for small orders. We closely collaborate with clients to modify existing designs and explore new possibilities, ensuring they fully benefit from additive manufacturing.
Laser-Powder Bed Fusion Equipment
Elmet Technologies is committed to advancing innovation through significant investments in the research and development of specialty additive refractory powders. Our cutting-edge Renishaw Laser-Powder Bed Fusion printer showcases the future of 3D printing with materials like tungsten, rhenium, niobium, tantalum, and molybdenum
Renishaw AM400 – Laser PBF Printer
- Build Volume: 250 x 250 x 280 mm (9.8 x 9.8 x 11 in tall)
- Maintains <100 ppm oxygen in the build chamber for optimal material integrity.
- Reduced build volume insert allows printing of custom alloys in small batches (5-10kg).
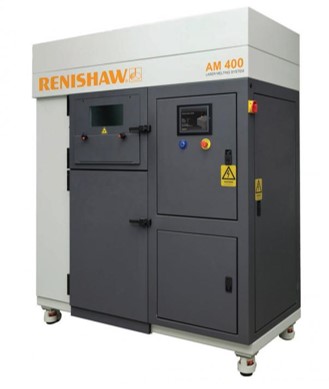
Powder Production
Spray Dry & Plasma Densification
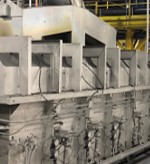
Pure W and Mo Powder Production
Fully integrated hydrogen reduction and blending of alloys
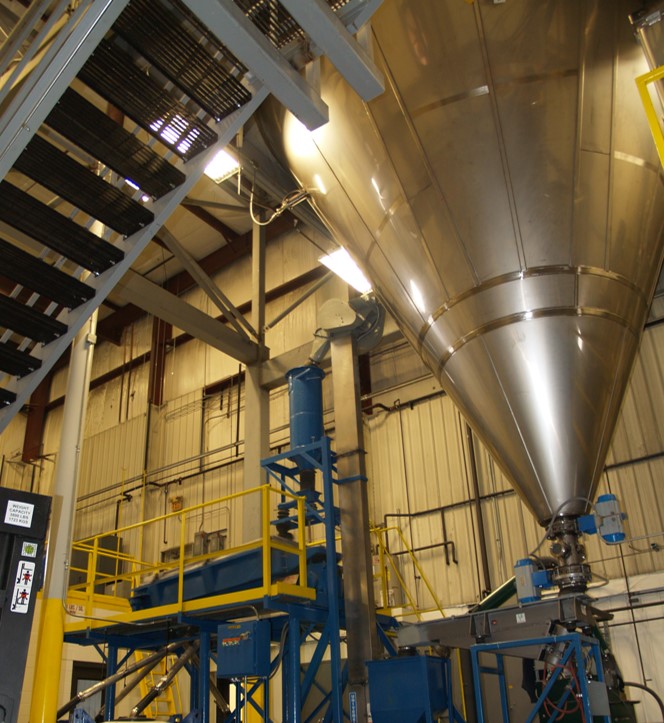
Multiple Spray Drying
Units of different sizes to spheroidize alloyed or pure powders with a binder
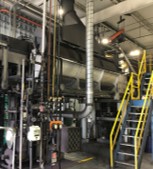
Sintering
Hydrogen sintering
removes binder, strengthens particles for plasma processes
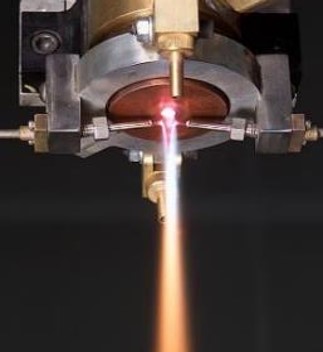
Plasma Process
Internal plasma melting units at 20,000 degrees to fully densify spheres
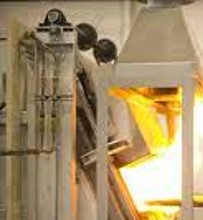
Post-Plasma
Post-plasma hydrogen sintering
lower surface oxygen to the lowest possible
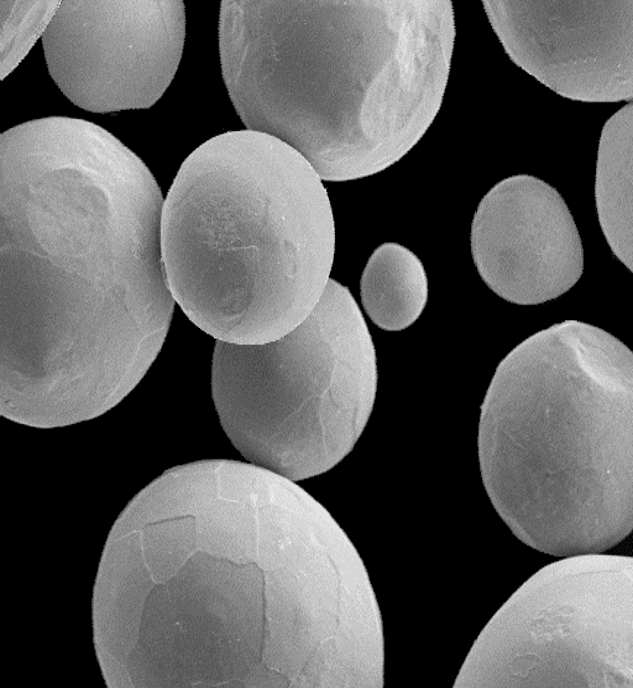
Screen, Test & Package
Full product lab inspection and packaging (in house SEM)
Laser – Powder Bed Fusion Applications
AEROSPACE

BIOMEDICAL
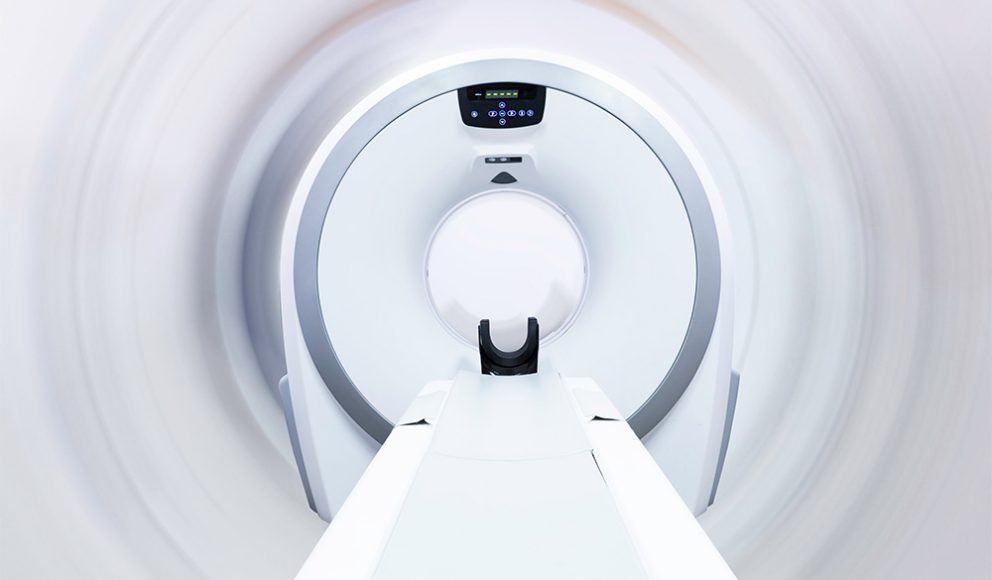
COLLIMATORS
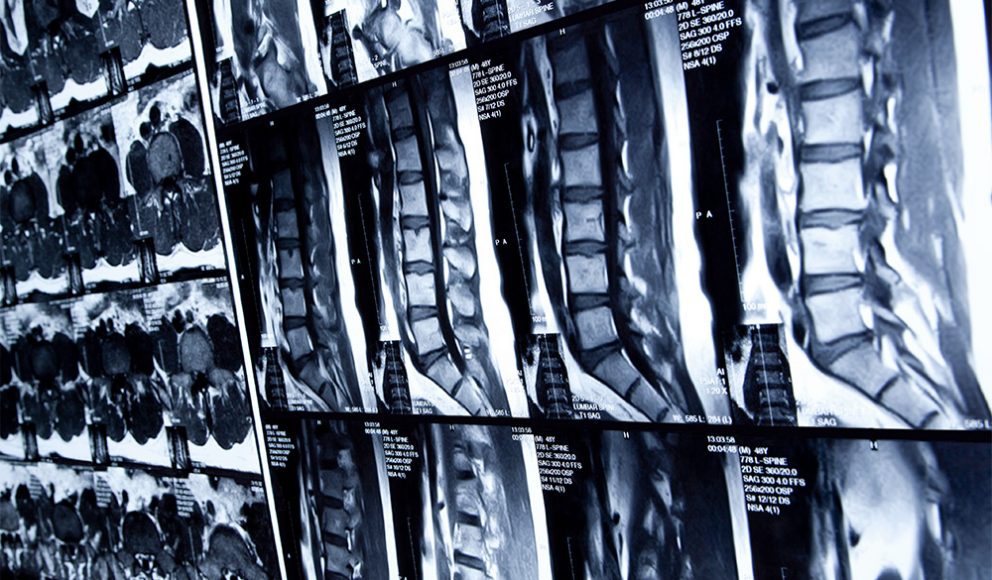
DEFENSE PARTS
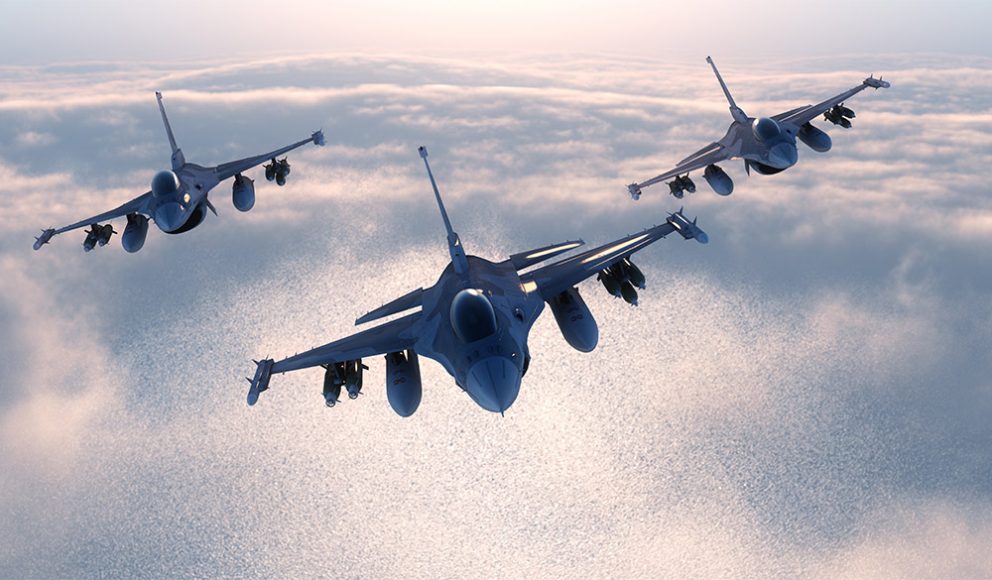
HEAT SHIELDS
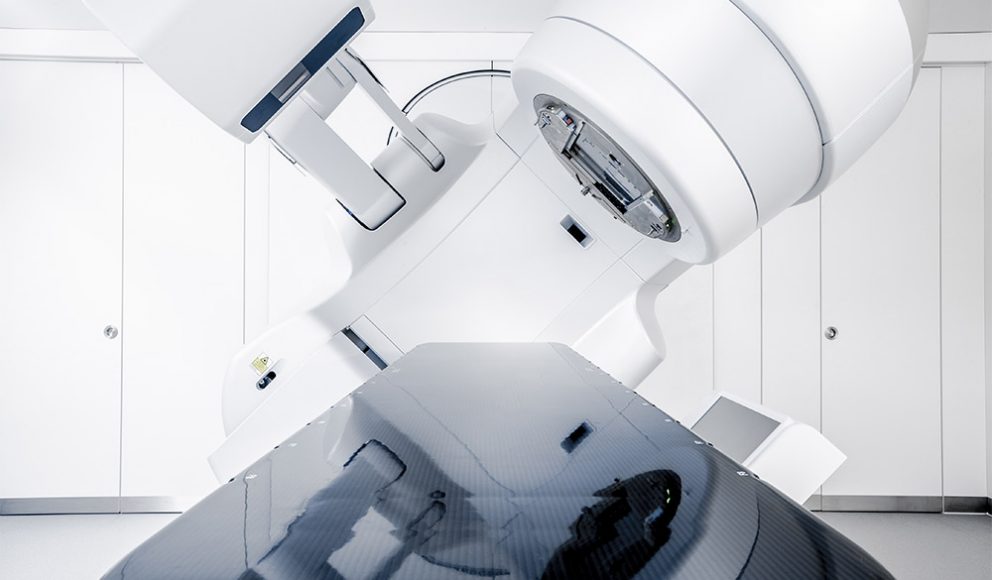
Powder Bed Fusion materials
Below is a list of Laser-Powder Bed Fusion materials we currently have as well as materials that are currently in development:
- Production ready and R&D materials: W, WHA, WRe, Ta W, Mo, MoRe, Re, TZM, Nb, C103, Ta, Ta-5W
Laser – Powder Bed Fusion: Specifications and dAta
Property | Unit | Nb | Mo | Ta | W |
Purity | % | >99.95 | >99.95 | >99.95 | >99.95 |
Mean Particle Size D50 | µm | 25-35 | 25-35 | 25-35 | 25-35 |
D10/D90 | µm | 15/45 | 15/45 | 15/45 | 15/45 |
Bulk Density | g/cc | 4 | 5 | 8 | 10 |
Hall Flow | s/50g | 14-16 | 8-10 | 5-9 | 5-8 |
Oxygen | ppm | 1500 | 400 | 300 | 250 |

Advantages of Powder Bed fusion
L-PBF offers several benefits, including cost savings and reduced material waste due to its efficient use of resources. It speeds up production development and supports rapid prototyping and small-batch manufacturing. This technology can create parts with varying properties and allows for complete customization. It delivers high resolution, efficiently recycles unused powder, and can combine different metal materials. Additionally, it eliminates the need for machining fixtures, making it a versatile and cost-effective manufacturing solution.
Global Leader in Additive Manufacturing
Elmet Technologies, founded in 1929, is a global leader in tungsten and molybdenum refractory metal products. Specializing in advanced manufacturing techniques like 3D printing, powder metallurgy, and alloy development, Elmet delivers high-quality, custom solutions with a steadfast commitment to innovation and customer support, making it a trusted partner for industries worldwide.